Safety Light Curtain from Pinnacle Systems
MicroGuard® Light Curtain with Metal Box Controller
The MicroGuard® safety light curtain utilizes the diverse redundancy design concept. This gives the safety light system a higher level of redundancy and control reliability. The two microprocessors are of different design, and the microprocessor or parallel programs are run and made up from different instruction sets written by different programmers.
The MicroGuard® safety light curtain self-checks every 20 milliseconds. Self-checking is the ability to electronically verify that all of the systems’ critical internal circuit components and their redundant counterparts or back-ups are operating properly.
The MicroGuard® provides two methods of cross monitoring design. One utilizes two microprocessors and two captive contact relays and the other uses four watchdog timers monitoring the system and the captive contact relays.
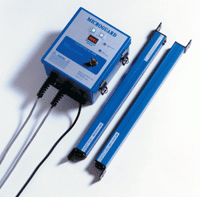
Model SS Solid State Safety Light Curtain
The Model SS is an infrared safety light curtain that is designed to the IEC 61496 standard. When properly installed, it protects the machine operator by passing an invisible infrared light beam across an area to be guarded and examining whether or not the light beam(s) are blocked. If the light beam(s) are blocked, monitored solid state outputs will open, issuing a “STOP” command to the machines normally closed (N.C.) “STOP” circuit. The System is composed of a transmitting unit (EMITTER), and a receiving unit (RECEIVER). The entire system is control reliable Category 4 (per IEC 61496). A single fault anywhere within the Model SS will not prevent at least one of the solid state outputs from opening up, (allowing a “STOP” command) when either a beam is broken or an internal fault occurs.
The Model SS protects an area by projecting a curtain of infrared light. The infrared emitters and receivers face each other across the field to be protected. Each emitter/receiver pair is spaced along the length of the pylons at regular intervals from .5″, up to 8″ depending on the application. The smaller spacing are for finger guarding, the larger spacing are for body protection. The emitter/receiver pairs are scanned sequentially (one at a time) by a very short pulse of infrared light starting from bottom (cable end), and working up to the top, until every beam pair has been scanned. Two 16 bit computers in the emitter pylon and two 16 bit computers in the receiver pylon control the operation, as well as cross check each pylon.
The Model SS employs infrared technology in a small sealed NEMA 4 aluminum housing with an infrared passing (daylight filtering) acrylic lens. This system provides harmless invisible protection and an unobstructed view of the guarded area. There are two parts to the Model SS: An Emitter pylon and a Receiver pylon. The Emitter pylon has no outputs but does contain a digital CAN data network to allow it to be linked to the Receiver pylon (although not required for operation). The Receiver pylon contains the digital CAN data network and two monitored solid state 24vdc outputs. Both pylons are synchronized to each other either via the CAN data network or electronically.
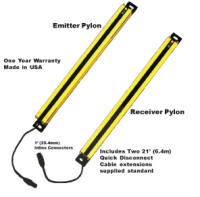
Model CA Cascading Safety Light Curtain
Cascading safety light curtains provide the user with the ability to connect additional sets of light curtains by daisy chaining multiple emitters and receivers together.
The cascading of safety light curtains provides multiple areas of guarding in any plane (X, Y, Z) while utilizing the control reliable dual safety outputs from the Category 4 safety device for the safety outputs to the machine control.
The ability to guard multiple areas on irregular shaped machines by cascading safety light curtains reduces wiring and provides a lower cost yet effective machine guarding solution.
The Model CA Cascading Safety Light Curtain is an infrared safety light curtain that is designed to the IEC 61496 standard. When properly installed, it protects the machine operator by passing an invisible infrared light beam across an area to be guarded and examining whether or not the light beam(s) are blocked.
If the light beam(s) are blocked, monitored solid state outputs will open, issuing a “STOP” command to the machines normally closed (N.C.) “STOP” circuit. The CA System is composed of transmitting units (EMITTERS) and receiving unit (RECEIVERS). The entire system is control reliable Category 4 (per IEC 61496). A single fault anywhere within the Model CA will not prevent at least one of the solid state outputs from opening up, (allowing a “STOP” command) when either a beam is broken or an internal fault occurs.
Model PPG Perimeter Guarding Light Curtain
Perimeter Guards utilize wider beam spacing than safety light curtains protecting personnel from “pinch point” or “point of operation” hazard zones. Perimeter Guards are designed to detect when an operator or passerby penetrates the perimeter of a hazardous zone. The Perimeter Guard safety light curtain will then initiate a stop signal to the machine control.
Perimeter Guards also incorporate latching safety relays. This requires a manual reset after each penetration into the guarded zone. This is an additional safety feature to protect the intruder from an inadvertent machine actuation while the intruder is within the work area.
Options include cornering mirrors and mounting pedestals.
Through the use of cornering mirrors, multiple sides or work envelopes can be guarded which enhance safety and reduce downtime related to mechanical and electrical interlock systems. Include a 5% reflectivity loss per mirror when calculating total scanning distance of light curtain.
The heavy duty, all welded steel pedestal floor mounts can be used for mounting either light curtain pylons or cornering mirrors. Sliding mounts on the pedestal are of universal design and are supplied standard. Unique floating base on a pedestal is designed to compensate for uneven floors.
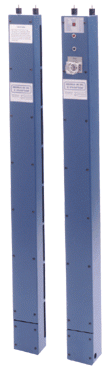